When choosing a stone veneer style for your project, one of the biggest decisions you will make is whether you want mortar joints or a dry-stack look. Both offer advantages but require a different installation process to achieve a polished result. Visit Concrete Stonefacing for more information.
Always ensure your concrete or CMU/Poured-in-place walls are fully cured before installing stone veneer. Moisture control is critical to prevent efflorescence, which is the leaching of minerals into your stone cladding application.
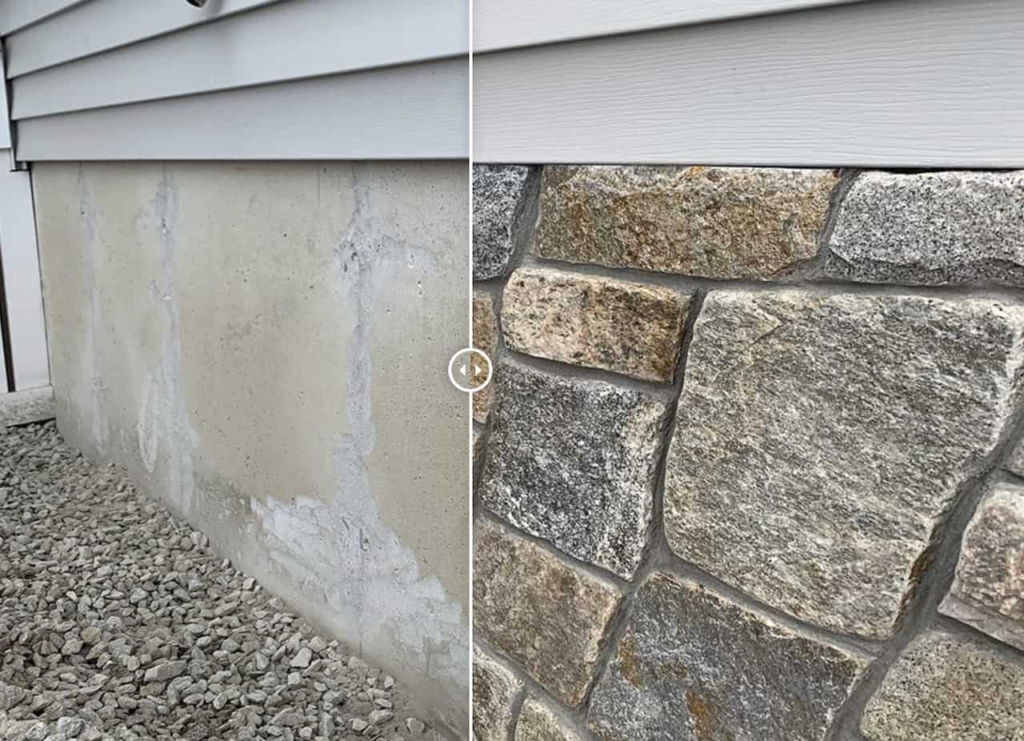
Split-face concrete block is a popular choice in the commercial building industry. It can transform a wall into a layered work of art with its natural cleft texture that mimics the look of stone masonry. Split face blocks are available in various colors, including traditional stone-color greys, browns, and tans. They are also fire-rated for up to four hours by ASTM C90.
The blocks are molded face-to-face and then mechanically split to expose the internal aggregates. The aggregates are then sized and colored to achieve the desired aesthetic, giving split-face concrete blocks a distinctive look. While this type of block is pricier than a smooth concrete block, achieving that beautiful textured look for your project is worth the extra expense.
As with all concrete masonry, moisture intrusion is a real concern. While many properly constructed buildings with Renaissance stone or other decorative masonry have no issues with moisture, severe damage is more common in older homes and newer commercial structures built using split face block and concrete masonry units (CMU) and mortared with Portland cement.
Moisture damage in block structures is primarily caused by water wicking through the porous construction and evaporating into the structure. This creates a pressure imbalance that can lead to structural damage.
The simplest solution to preventing this problem is through proper waterproofing and moisture control techniques. This includes using proper flashings, self-adhered flashings, and a quality masonry sealant. Using the right type of mortar for your project is also essential. A good waterproofing mortar should have a latex additive to prevent water penetration.
Lastly, be sure to hire a reputable contractor. Compare at least three quotes before choosing a company, and check online reviews and experience. Ask for an itemized bid listing all costs; never pay in full upfront. This will help avoid shoddy artistry and other common problems associated with unlicensed contractors. Choose a licensed contractor with at least five years of experience for the best results. This will ensure you get the highest-quality artistry possible, ensuring your project’s longevity and durability.
Concrete sculpture is a creative and easy way to add beauty to your outdoor spaces. First, you must prepare a latex, aluminum, styrofoam, or plaster mold. Then, you must mix cement with other ingredients to create high-quality and durable concrete. Once you have the concrete ready, pour it into the mold and let it dry a bit. After this, you can begin carving your masterpiece. When you’re done, let it cure for a few days before you remove the mold.
Sculptured concrete is usually applied to walls or vertical surfaces and can be used in waterfalls, outdoor kitchens and fireplaces, man caves, and wine cellars. It also can be incorporated into driveways and walkways to give them a natural stone look. The best part about sculpted concrete is that it costs less than natural stone and can be molded to look exactly how you want it to.
For the best results, use Marble’s concrete release agent to help you get your castings out of the molds without any gummy residue or interference with surface detail. The water-soluble release can be added to your mix before you start pouring and will not interfere with the concrete’s curing process or leave any air bubbles in your finished castings.
One of the most popular sculpted concrete forms is the split face, typically used on walls or columns. It’s a highly decorative style of concrete that gives your project the appearance of real stone and is available in a wide range of colors. It’s also durable and low-maintenance, making it a great choice for outdoor areas.
Another common type of sculpted concrete is tuckpointing, which involves repairing joints between stones with mortar. This is often done on older, existing concrete structures that are deteriorating or have cracks. The tuckpointing process is usually done by hand using a trowel and grout bag. However, several machines can do the job faster and more accurately.
To create the look of aged stone, you can use a concrete stain to color the concrete after it’s been poured. This will give the concrete a faded and weathered look that creates a rustic stone appearance.
Color-wash concrete stone facing is a technique that can be applied to new construction or existing structures. This popular technique transforms retaining walls, driveways, and other exterior surfaces. It can also create an interesting pattern on a patio or pool deck. This project is easy enough for an ambitious DIYer to undertake. Just be sure to mask off any areas you don’t want to stain properly and follow the steps outlined in this blog post for the best results. Once the color wash is dry, finish your project with a layer of Penetrating Sealer to protect the surface.
If you’re using a manufactured stone veneer, it is important to understand that the product’s color will lighten during the curing process. This is due to the moisture content in the mixture. The higher the moisture content, the darker and more saturated the appearance of the stone face will be, but it will eventually lighten. Depending on weather conditions and location, this process may take up to six months.
Staining and color treatments breathe life into new construction projects, transforming drab buildings and public spaces. Whether the structure is a city skyscraper, a museum, or an airport terminal, Nawkaw’s color treatments are in use worldwide.
Natural stone is a durable material, but it can be susceptible to damage from the elements. During construction, it is vital to use proper protective measures, including sealing and cleaning, to ensure your stones will last a lifetime.
Cleaning stonework is a delicate task that requires gentle cleaning products. Avoid harsh cleansers that contain acid, ammonia, or bleach. Instead, use a mild dishwashing detergent and a soft brush or sponge. If the stone is outside, wet it with a hose to remove dirt and debris.
A popular DIY project is a faux stone wall, which can be done with a stencil and concrete overlay. This is a great way to add character and value to your home without the expense and weight of real stone.
Concrete Stonefacing is a popular siding material for retaining walls and fireplaces. It comes in various textures and can mimic the look of natural stone or be used to create an entirely new style. Many contractors offer concrete stone veneer installation services, but hiring a company with experience and a strong track record of success is important. In addition, it is essential to prepare the site before installing stone veneer, as this will help prevent water damage and ensure that your project is structurally sound for the life of the project.
Manufactured stone is a slurry of Portland cement, aggregates, and iron oxides baked in textured molds to look like real stone. This material is a great alternative to real stone, as it is more affordable and has similar strength and durability. It can also be customized to meet the specific needs of your project. In addition, it can be easily colored and has a wide range of texture options.
Real stone is more expensive than manufactured stone but offers a unique appearance that cannot be replicated with other materials. Each piece of stone has its distinct colors, textures, and patterns, which can enhance the beauty of your home and increase its value. In addition, real stone is a natural insulator and helps to keep the house cool during the summer months.
Before installing stone veneer, you should cover the entire area with a waterproofing barrier. Next, a metal lath should be placed over the barrier and nailed into the studs in a shingle fashion. The local building code should do this. Next, the lath should be coated with a scratch coat of mortar cement mix, creating a surface to which the thin stone veneer can adhere.
If your project is in a moisture-prone environment, it is recommended that you treat the manufactured stone with a silane-based, non-film-forming masonry sealer. This will help protect the material from chemicals, such as chlorine, that can cause discoloration. It is also a good idea to hose down the surfaces occasionally to remove any accumulated dirt or debris.